Neodymium magnets, known for their exceptional strength and versatility, are vital components in a range of applications from electronics to renewable energy systems. This article delves into the detailed manufacturing process of these powerful magnets, highlighting each critical step and the equipment involved.
Table of Contents
Step 1: Raw Material Preparation and Pretreatment
The journey begins with the careful selection and preparation of various raw materials, including neodymium, praseodymium, boron, copper, aluminum, gallium, terbium, cobalt, iron, dysprosium, and niobium. Given the sensitivity of these materials to oxidation, especially those prone to it, descaling and precise weighing according to the material recipe are essential. This phase employs electronic scales, cutting machines, and descaling and polishing machines. Key control points in this step include accurate weighing, material proportioning, and thorough surface cleaning.
Common Elements in Neodymium Magnets
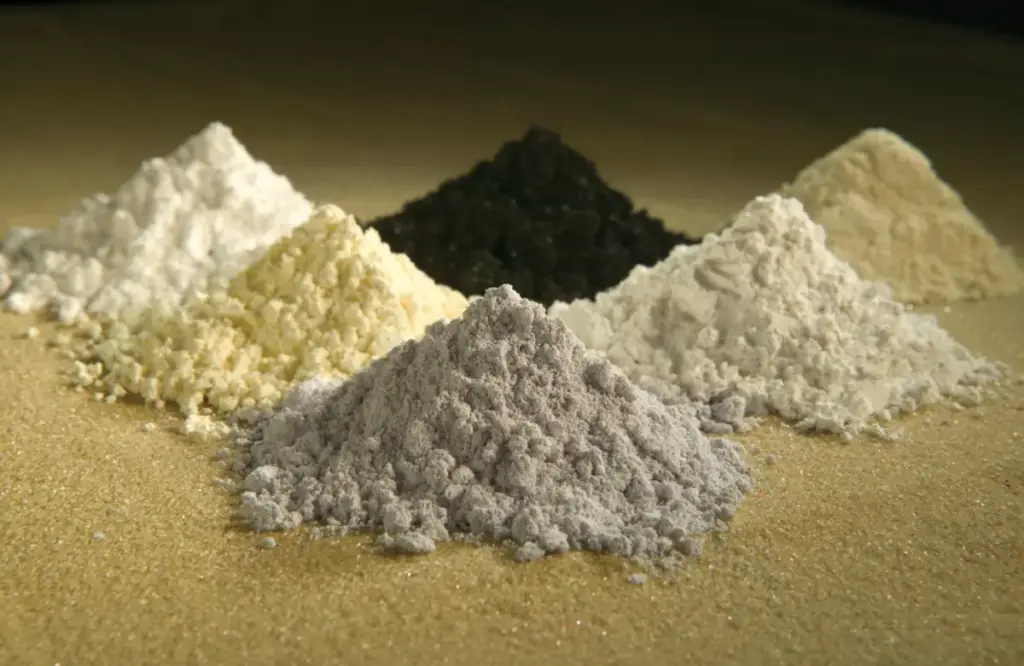
Neodymium magnets, or NdFeB magnets, are made from an alloy of neodymium, iron, and boron (Nd2Fe14B). The properties and performance of these magnets can be tailored by adjusting the composition and adding various elements. Different grades of neodymium magnets exhibit unique characteristics depending on the specific elements used. Here’s an overview of some common elements and their effects on different grades of neodymium magnets:
- Neodymium (Nd): Primary rare earth element. Essential for high magnetic strength and performance.
- Iron (Fe): Main component of the magnetic alloy. Contributes to the overall magnetic properties and structure.
- Boron (B): Stabilizes the crystal structure. Enhances the magnetic properties and thermal stability.
- Dysprosium (Dy): Increases the intrinsic coercivity, especially at high temperatures. Used in high-temperature environments such as electric motors and generators.
- Terbium (Tb): Similar to dysprosium, it enhances high-temperature coercivity. High-performance applications requiring thermal stability.
- Cobalt (Co): Improves resistance to oxidation and enhances magnetic properties at high temperatures. High-temperature and high-performance applications.
- Praseodymium (Pr): Can be used to partially replace neodymium, often to reduce costs while maintaining performance. General-purpose and cost-sensitive applications.
- Niobium (Nb): Enhances grain refinement, leading to improved magnetic properties and stability. High-performance applications.
- Aluminum (Al): Improves the corrosion resistance and mechanical properties. Applications where environmental resistance is critical.
- Gallium (Ga): Enhances the corrosion resistance and helps in the fine grain structure of the alloy. Applications requiring improved environmental resistance.
- Copper (Cu): Used to improve the thermal stability and reduce the grain size. Applications needing enhanced thermal and mechanical properties.
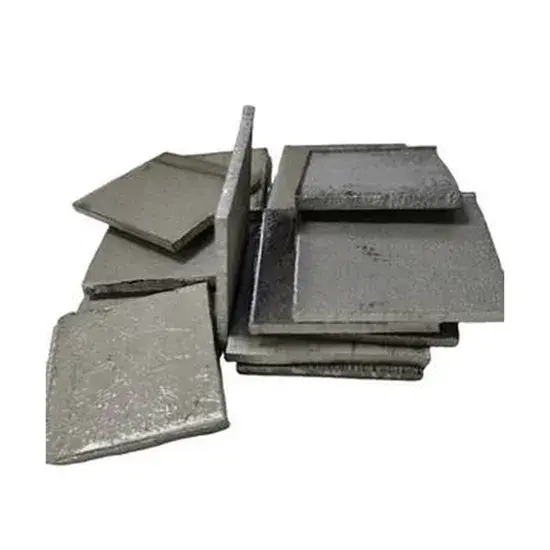
The specific combination and proportion of these elements determine the grade and characteristics of neodymium magnets. By tweaking the composition, manufacturers can produce magnets with tailored properties suitable for a wide range of applications, from consumer electronics to industrial machinery and beyond. Understanding these variations helps in selecting the right magnet grade for specific needs.
Step 2: Strip Casting
Initially, vacuum melting furnaces were the norm in China for melting the prepared materials, suitable for low-performance NdFeB magnets. However, as demand for higher performance grew, strip casting became necessary. This technique enhances the volume percentage of Nd2Fe14B in the main phase, improves grain orientation, and maintains about 2% of a neodymium-rich phase to ensure coercivity. By minimizing the formation of α-Fe during casting, the method directly generates the Nd2Fe14B phase, suppressing unwanted α-Fe precipitation.
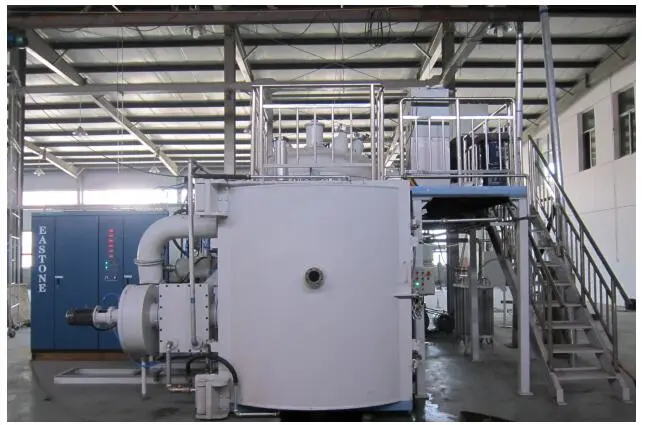
Strip Casting vs Traditional Casting
The strip casting process is superior to the traditional casting process in neodymium magnet manufacturing for several reasons. These advantages are primarily related to the enhanced control over the microstructure and composition of the alloy, leading to improved magnetic properties and performance. Here’s a detailed look at why strip casting is preferred:
Improved Microstructure Control
Grain Size and Orientation:
- Traditional Casting: Often results in larger, irregular grains and less uniformity in the microstructure.
- Strip Casting: Produces finer, more uniform grains with better orientation. This fine-grained structure is crucial for enhancing the magnetic properties of the NdFeB alloy.
Phase Composition:
- Traditional Casting: Can lead to the formation of undesirable phases such as α-Fe, which negatively impacts magnetic performance.
- Strip Casting: Helps prevent the formation of α-Fe by promoting the direct formation of the Nd2Fe14B phase, which is essential for high magnetic strength. This results in a higher volume percentage of the desired Nd2Fe14B phase.
Enhanced Magnetic Properties
Higher Coercivity:
- Traditional Casting: Often struggles to maintain high coercivity, especially at elevated temperatures.
- Strip Casting: Ensures a more consistent distribution of neodymium-rich phases, which enhances the intrinsic coercivity of the magnets. This is particularly important for applications requiring high-temperature stability.
Higher Remanence:
- Traditional Casting: May not achieve the highest possible remanence due to irregular grain size and phase distribution.
- Strip Casting: Produces magnets with higher remanence, resulting in stronger magnetic fields.
Reduced Oxidation and Contamination
Controlled Environment:
- Traditional Casting: The open-air or less controlled environment can lead to oxidation and contamination of the alloy, which degrades the magnetic properties.
- Strip Casting: Typically performed in a vacuum or controlled atmosphere, significantly reducing oxidation and contamination risks. This ensures higher purity and consistency in the final product.
Efficiency and Yield
Material Utilization
- Traditional Casting: Often involves more material waste due to the need for additional processing steps to achieve desired properties.
- Strip Casting: More efficient in material usage, reducing waste and improving overall yield. The process is designed to produce near-net-shape products, minimizing the need for extensive post-casting machining.
Consistency and Reproducibility:
- Traditional Casting: Variability in the casting process can lead to inconsistent quality in the final magnets.
- Strip Casting: Provides better control over the cooling rate and solidification process, resulting in more consistent and reproducible magnetic properties across batches.
Cost-Effectiveness
Reduced Post-Processing:
- Traditional Casting: Often requires extensive post-processing to achieve the desired microstructure and magnetic properties.
- Strip Casting: Reduces the need for extensive post-processing, lowering production costs and time.
Strip casting offers numerous advantages over traditional casting in the manufacturing of neodymium magnets. By providing better control over the microstructure, reducing oxidation and contamination, improving magnetic properties, and enhancing efficiency, strip casting significantly improves the quality and performance of NdFeB magnets. This makes it the preferred method in modern magnet manufacturing, particularly for high-performance applications requiring superior magnetic characteristics.
Step 3: Hydrogen Crushing
Post-melting, the material sheets are exposed to hydrogen, leveraging the hydrogen absorption property of rare earth metals. Hydrogen enters the alloy along the neodymium-rich phase, causing it to expand and crack, turning the sheet material into coarse powder. This coarse powder is uniformly mixed in a stirring tank, preparing it for the next stage.
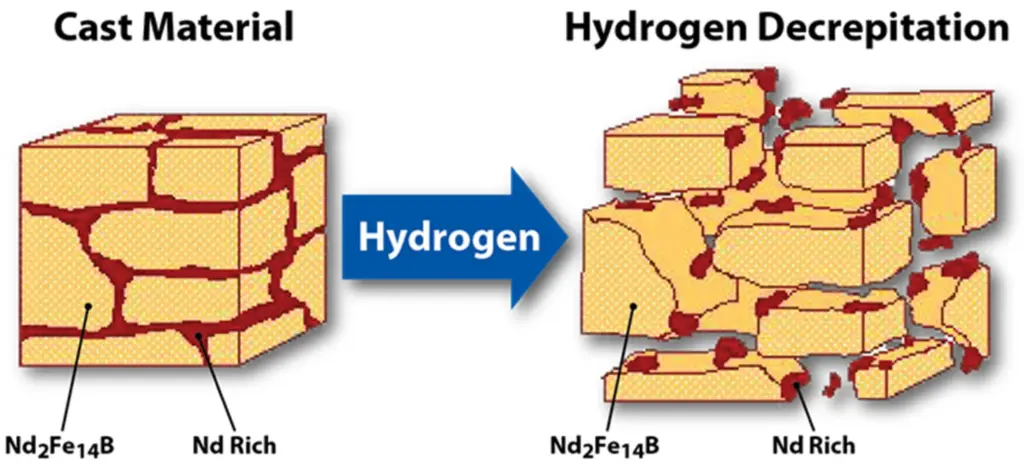
Hydrogen crushing, also known as hydrogen decrepitation, is a crucial step in the neodymium magnet manufacturing process. This method offers several advantages over traditional mechanical crushing methods. Here are the key benefits of hydrogen crushing in the context of neodymium magnet production:
- Improved Particle Size Control: Produces more uniformly sized particles, which is essential for the subsequent sintering process. Uniform particle size ensures better packing density and homogeneity in the final magnet.
- Enhanced Microstructure, Leads to finer and more controlled grain sizes. This refinement is crucial for achieving superior magnetic properties in the final product.
- Reduced Mechanical Stress, Uses hydrogen absorption and subsequent expansion to break the material along the neodymium-rich phase. This method induces less mechanical stress and damage compared to traditional mechanical crushing.
- Improved Process Efficiency, Generally requires less energy compared to mechanical crushing methods, as it leverages the material’s natural properties to facilitate breaking.
- Enhanced Material Handling, Produces powder that is easier to handle and mix uniformly in subsequent processes. This uniformity is vital for achieving consistent quality in the final magnets.
- Improved Quality Control, Allows for more precise control over the particle size and distribution, leading to better control over the final magnetic properties.
- Reduced Need for Hazardous Substances, the Traditional Crushing may involve processes that require hazardous substances for cooling or lubrication, posing environmental and safety risks. Hydrogen Crushing, Typically does not require the use of hazardous chemicals, making it a more environmentally friendly option.
Step 4: Airflow Mill Grinding
The coarse powder undergoes further size reduction through high-pressure airflow, where particle collisions create fine powder. This stage requires strict oxygen exclusion to prevent oxidation, using nitrogen-filled containers and bagging. Particle size testing ensures the fine powders meet process requirements, and different grades are mixed according to the composition ratio.
Airflow mill grinding, also known as jet milling, is a crucial process in the manufacturing of neodymium magnets. This technique involves the use of high-pressure air to grind materials into fine powders. Airflow mill grinding uses high-pressure air or gas to accelerate particles and cause them to collide with each other, resulting in the breakdown of the material into fine powder.
- Particle Size Reduction,The process is designed to produce extremely fine particles, often in the range of micrometers. This fine powder is essential for the uniformity and quality of the final sintered neodymium magnet.
- Oxygen Exclusion, To prevent the powder from oxidizing, the entire process is conducted in an inert atmosphere, usually nitrogen. Containers and bags used to handle the powder are also filled with nitrogen to maintain the inert environment.
Airflow mill grinding is a critical step in the manufacturing of neodymium magnets, offering significant advantages over traditional grinding methods. By producing fine and uniform particles, enhancing magnetic properties, improving the sintering process, and maintaining a controlled environment, airflow mill grinding ensures the production of high-quality neodymium magnets. This method’s efficiency and consistency make it indispensable in modern magnet manufacturing, contributing to the superior performance of neodymium magnets in various applications.
Step 5: Press Forming
The press forming process is a critical stage in the manufacturing of neodymium magnets. This step shapes the powdered material into a preliminary form, typically a simple block or cylinder, before sintering and final machining. The process ensures that the pre-formed compacts have the desired density and particle alignment, which are essential for the final magnetic properties.
Press forming for NdFeB differs from that of sintered Alnico magnets, requiring orientation during the process. The magnets are formed into simple shapes like squares or cylinders using a press machine with magnetic field and demagnetization devices. The mold consists of an upper and lower cylinder; the powder is weighed, caved, and then pressed with electromagnetic orientation. After holding pressure and demagnetizing, the upper cylinder retracts, and the lower cylinder pushes the formed product out. Density, weight, and size are critical quality indicators, regularly inspected to ensure consistency.
Key Aspects of Press Forming
- Powder Preparation: The fine neodymium, iron, and boron powder, often mixed with other elements like dysprosium or terbium, is carefully prepared. This powder is the result of previous processes such as hydrogen crushing and airflow mill grinding.
- Orientation: Unlike some other types of magnets, neodymium magnets require the powder particles to be oriented in a magnetic field during pressing. This orientation aligns the magnetic domains, enhancing the magnetic properties of the final product.
- Press Machine Design: The press machine used for neodymium magnets includes components for applying both mechanical pressure and a magnetic field. The mold typically consists of an upper and lower cylinder.
Steps in the Press Forming Process
- Filling the Mold: The prepared powder is carefully weighed and placed into the mold. The amount of powder is crucial to achieve the desired density and preliminary dimensions of the magnet.
- Applying the Magnetic Field: A magnetic field is applied to orient the powder particles. This step is essential for maximizing the magnetic properties of the finished magnet.
- Compressing the Powder: The upper cylinder presses down on the powder, compressing it into a simple shape like a block or cylinder. The pressure must be controlled precisely to ensure uniform density and avoid defects.
- Holding Pressure: The pressure is held for a specific amount of time to ensure that the powder particles bond together effectively. During this time, the magnetic field continues to maintain the orientation of the particles.
- Release mold: After the powder has been sufficiently compressed, the magnetic field is turned off, and the upper cylinder retracts. The lower cylinder then pushes the formed compact out of the mold.
- Inspection and Quality Control: The formed compacts are inspected for density, weight, and dimensions. Consistency in these parameters is crucial for the subsequent sintering process and the overall quality of the magnets.
Step 6: Cold Isostatic Pressing
In cold isostatic pressing, the semi-finished NdFeB block is subjected to ultra-high pressure in a closed container filled with oil. This process enhances product density, crucial for subsequent sintering and overall magnetic performance. The density increase from cold isostatic pressing directly impacts the magnet’s efficiency.
Cold isostatic pressing (CIP) is a critical step in the manufacturing of neodymium magnets, used to enhance the density and uniformity of the pre-formed compacts before sintering. This process involves applying high pressure uniformly in all directions using a liquid medium, typically oil or water, to compress the material.
- Enhanced Density and Uniformity, achieves higher and more uniform density throughout the compacts, crucial for optimal magnetic properties and mechanical strength.
- Improved Magnetic Properties, The uniform density and reduced porosity enhance the magnetic performance of the neodymium magnets, leading to higher coercivity and remanence.
- Elimination of Internal Defects, Reduces internal defects such as pores and cracks, which can compromise the structural integrity and performance of the magnets.
- Flexibility in Shape and Size, Can be used for compacts of various shapes and sizes, providing flexibility in the manufacturing process.
Step 7: Sintering Process
Sintering, a pivotal process for NdFeB magnets, occurs in a vacuum sintering furnace and includes a heat treatment phase. Initially, the furnace cavity is vacuumed and heated to around 800˚C before further heating and exhausting to remove gases within the product. The sintering occurs at approximately 1200˚C for over four hours, followed by heat treatment at about 900˚C for two hours and then at 550˚C for five hours. Temperature control varies slightly for different grades, but the general process remains consistent.
The sintering process is a critical stage in the manufacturing of neodymium magnets. This process involves heating the pressed and cold isostatically pressed (CIP) compacts to high temperatures in a vacuum furnace to bond the particles together, enhance the magnetic properties, and achieve the desired density and mechanical strength.
- Vacuum Environment: The sintering process is conducted in a vacuum or inert gas atmosphere to prevent oxidation and contamination of the neodymium magnets. This ensures the purity and quality of the final product.
- Controlled Heating: The compacts are subjected to a carefully controlled heating schedule, including a series of temperature ramps, holds, and cool-down periods to achieve the desired microstructure and magnetic properties.
- Heat Treatment: In addition to sintering, the process often includes specific heat treatment steps to optimize the magnetic properties and mechanical strength of the magnets.
Steps in the Sintering Process
- Loading the Furnace: The pre-formed and CIP-compacted neodymium magnet blanks are placed into the vacuum furnace. The furnace is then evacuated to create a vacuum environment, typically reaching pressures as low as 4.2E-2 Pa.
- Initial Heating Phase: The furnace is gradually heated to a temperature of around 800°C. This initial heating phase helps to remove any residual gases and moisture trapped within the compacts.
- High-Temperature Sintering: The temperature is then increased to the sintering temperature, typically around 1200°C, and held for an extended period (about 4 hours). During this phase, the particles bond together to form a solid, dense structure.
- Cooling Phase: After the sintering hold, the temperature is gradually reduced. This controlled cooling helps to prevent thermal stresses and cracks in the material.
- Heat Treatment: Following the sintering phase, a heat treatment stage is often conducted. This includes holding the magnets at around 900°C for 2 hours and then at 550°C for 5 hours. The heat treatment helps to optimize the magnetic properties, particularly the coercivity and remanence.
The sintering process is a vital step in the manufacturing of neodymium magnets, enabling the production of high-performance magnets with superior magnetic properties, mechanical strength, and uniformity. By carefully controlling the heating, holding, and cooling phases in a vacuum environment, manufacturers can achieve the optimal microstructure and density required for neodymium magnets. This process, combined with subsequent heat treatments, ensures that the magnets meet the stringent demands of various applications, from electronics to renewable energy systems.
Step 8: Machining
Neodymium magnets (NdFeB) are the strongest type of permanent magnets available, widely used in various high-performance applications. However, machining these magnets can be challenging due to their brittleness and susceptibility to oxidation. Proper techniques and precautions must be taken to ensure successful machining without compromising the magnet’s integrity.
Challenges in Machining Neodymium Magnets
- Brittleness: Neodymium magnets are brittle and prone to chipping or cracking during machining.
- Oxidation: They are highly susceptible to oxidation, which can degrade their magnetic properties.
- Magnetic Properties: Machining can generate heat, which might affect the magnetic properties of the magnets.
- Safety Concerns: The fine dust generated during machining is flammable and poses health risks if inhaled.
Machining Techniques
The primary machining techniques used for neodymium magnets include cutting, grinding, and drilling. Each technique requires specific tools and precautions.
Cutting:
- Wire EDM (Electrical Discharge Machining): This technique uses a thin wire to cut through the magnet with high precision. It is suitable for creating complex shapes without causing significant mechanical stress.
- Diamond-Coated Cutting Tools: Diamond-coated saws or cutting wheels can be used for cutting neodymium magnets. The use of coolant is essential to minimize heat generation and prevent oxidation.
Grinding:
- Diamond Grinding Wheels: Diamond grinding wheels are ideal for shaping and finishing neodymium magnets. Grinding should be done slowly to avoid excessive heat buildup.
- Coolant Use: Continuous use of coolant is necessary to keep the temperature low and prevent oxidation during the grinding process.
Drilling:
- Diamond-Coated Drill Bits: Diamond-coated drill bits are recommended for drilling holes in neodymium magnets. The drilling speed should be slow, and coolant should be used to prevent overheating.
- Avoiding Stress: Care should be taken to avoid applying excessive force, which can cause the magnet to crack or chip.
Recent advancements have significantly improved the machining of sintered NdFeB magnets. For small products, multi-wire cutting machines have replaced traditional wire cutting, enhancing efficiency. Special diamond tools are used for sinkhole products, while general sizes still employ wire cutting. As global demand for NdFeB magnets grows, so does the development of related equipment.
Step 9: Coating and Plating
Neodymium magnets (NdFeB) are renowned for their exceptional magnetic strength, but they are also prone to corrosion and oxidation. To enhance their durability and longevity, these magnets are often coated or plated with various materials. This process not only protects the magnets from environmental factors but also improves their performance in different applications.
Why Coating and Plating Are Necessary
Neodymium magnets are highly susceptible to oxidation, which can lead to degradation of their magnetic properties and structural integrity. The primary reasons for coating and plating neodymium magnets include:
- Corrosion Resistance: Protects the magnet from moisture and other corrosive elements.
- Durability: Enhances the mechanical strength and surface hardness of the magnet.
- Aesthetic Appeal: Improves the appearance of the magnet, making it suitable for consumer products.
- Lubricity: Reduces friction in applications where magnets come into contact with other materials.
Common Coating and Plating Methods
Various materials are used for coating and plating neodymium magnets, each offering different benefits. The most common methods include:
Nickel (Ni) Coating:
- Composition: Typically a triple layer of nickel-copper-nickel (Ni-Cu-Ni).
- Benefits: Provides excellent corrosion resistance, good mechanical strength, and a shiny, aesthetically pleasing finish.
- Applications: Widely used in consumer electronics, automotive parts, and industrial applications.
Zinc (Zn) Coating:
- Composition: A single layer of zinc.
- Benefits: Offers good corrosion resistance and is cost-effective. The finish is typically dull gray.
- Applications: Suitable for applications where cost is a concern, such as hardware and mechanical components.
Epoxy Coating:
- Composition: A layer of epoxy resin.
- Benefits: Provides excellent corrosion resistance and good insulation properties. Available in various colors.
- Applications: Used in applications where electrical insulation is required, such as sensors and electronic components.
Gold (Au) Plating:
- Composition: A layer of gold over a nickel base.
- Benefits: Offers superior corrosion resistance, excellent electrical conductivity, and a high-quality finish.
- Applications: Ideal for high-end electronic components and medical devices.
Silver (Ag) Plating:
- Composition: A layer of silver over a nickel base.
- Benefits: Provides good corrosion resistance and excellent electrical conductivity.
- Applications: Used in applications requiring high electrical conductivity, such as connectors and switches.
Phosphate Coating:
- Composition: A layer of phosphate compounds.
- Benefits: Provides moderate corrosion resistance and improves adhesion for subsequent coatings.
- Applications: Used as a base layer for other coatings or in applications where cost-effective corrosion protection is needed.
Parylene Coating:
- Composition: A thin, conformal coating of parylene.
- Benefits: Offers excellent chemical resistance, dielectric properties, and biocompatibility.
- Applications: Used in medical devices, electronics, and aerospace applications.
The final step addresses the poor anti-corrosion ability of NdFeB magnets. The neodymium-rich phase is susceptible to oxidation, leading to powder frothing. To combat this, sintered NdFeB magnets are coated or plated with anti-oxidation layers, commonly Zn, Ni, or NiCuNi. Before plating, the magnets undergo passivation to ensure long-lasting protection.
Coating and plating are essential processes for enhancing the durability, performance, and aesthetic appeal of neodymium magnets. By choosing the appropriate coating or plating method, manufacturers can ensure that neodymium magnets perform reliably in a wide range of applications, from consumer electronics to industrial machinery. Understanding the benefits and applications of each coating and plating method helps in selecting the best option for specific needs.
Conclusion
The meticulous process of manufacturing neodymium magnets combines advanced techniques and precise control measures to produce high-performance, durable magnets. Each step, from raw material preparation to the final coating, plays a crucial role in ensuring the magnets meet stringent quality standards. As technology and demand evolve, so too will the processes and innovations in neodymium magnet production.
Leave a Reply